By Lindsey Coulter
The Georgia Institute of Technology Athletics Department recently celebrated a milestone in the construction of the Thomas A. Fanning Student-Athlete Performance Center. On March 8, the project team and stakeholders gathered for the topping-out ceremony as the construction crew installed the center’s final steel beam. Interestingly, several of the steel members used in the 100,000-square-foot project already had a long history with the university.
Located in the northeast corner of Bobby Dodd Stadium at Hyundai Field, the Fanning Center is being constructed on the footprint of the former Edge/Rice Center. When complete, the Fanning Center will serve as a state-of-the-art hub for Georgia Tech student-athletes, offering new and improved strength and conditioning and sports medicine facilities as well as a sports science lab, nutrition services, and meeting and office spaces.
In addition to communicating the university’s commitment to student-athletes, the project also puts the institution’s sustainability values on display. Designed by the S/L/A/M Collaborative (SLAM), with Walter P Moore as structural engineer and constructed by DPR Construction, the project incorporated multiple carbon- and energy-reducing strategies. Most significantly, it included repurposing steel members from a portion of the Bobby Dodd Stadium’s upper deck that was demolished to establish the Fanning Center structure.
Ideation to Implementation
The project first broke ground in March 2024. During the planning process, however, the Walter P Moore team recognized a unique opportunity to sustainably reclaim steel members from the stadium to reduce carbon emissions and promote sustainable design.
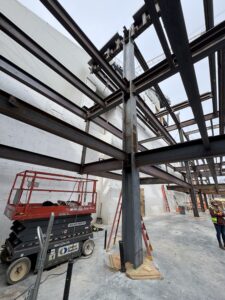
Photo Credit: Courtesy of Walter P Moore
The goals were to repurpose the existing structural elements without compromising the project timeline or budget, to improve material circularity, to reduce waste and to significantly lower the project’s embodied carbon footprint. This required seamless collaboration between Green Circle Demolition and DPR Construction managers to ensure the salvage, refabrication and integration of the steel beams into the new structure was successful.
Team members had a unique advantage in that they were able to study the stadium plans and develop a solid strategy for removing, refabricating and reusing the steel beams.
“Steel reclamation, salvage, deconstruction and reuse are not common practices,” said Kelly Roberts, PE, SE, LEED AP BD+C, principal and managing director of Walter P Moore. “Typically, steel is recycled, and when a building is being demolished, you’ll separate out the metals because they have a very high recycled value.”
To be recycled, steel is melted down in furnaces that are heated to at least 3,000 degrees Fahrenheit, a highly energy-intensive process, after which the steel is most often recast and rerolled into new steel shapes. In contrast, the team developed a strategy to remove the steel from the stadium structure, transport it to a local fabrication shop to receive new connection material and then return it to the project site for use in the new Fanning Center. While the process sounds straightforward, it required extensive pre-planning, collaboration and documentation review as well as group site walks to get all members on the same page.
Reimagining Materials
Most of the steel members that were good candidates for reuse were part of the raker system of the upper deck of the stadium, according to Will Childs, P.E., S.E., project manager at Walter P Moore.
“Those were taken from being sloped or trussed members, supporting seating units, and then taken down and cut into shorter lengths, then reused as a beam or column in the new building,” Childs said.
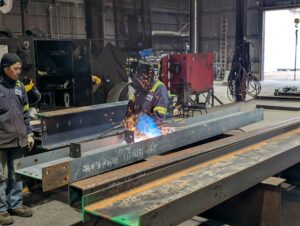
Photo Credit: Courtesy of Walter P Moore
The team also evaluated whether salvage from an adjacent building that also being demolished, the Edge-Rice Building, was possible. However, much of that steel was composite, meaning it had been cast integrally with the steel deck and concrete above as part of the floor.
“That’s actually something that the steel industry is researching right now: how to make more steel salvageable and develop some best practices to make sure we can get the most out of salvage, deconstruction and reuse to make this approach more widespread,” Roberts said.
In the meantime, Roberts encourages teams that are considering similar strategies to begin conversations as early as possible with all project partners. As the value of demolition steel is often factored into the demolition subcontractor’s contract, having the conversation early can help address financial and contractual questions in a timely manner.
“In this case, we also got the construction manager at-risk involved early,” added Marc Clear, AIA, LEED AP BD+C, principal and national market leader with SLAM. “They were hired just a few weeks after the design team. A design-build method could also deliver that capability, but having the demolition scope as part of the primary project was key.”
Ultimately, the salvage effort was cost- and schedule-neutral; however, the sustainability benefits were clear. According to the team’s calculations, the strategy saved approximately 25,000 kilograms of carbon dioxide, which is roughly equivalent to 60,000 miles driven by an average gas-powered vehicle.
When the project is completed in spring 2026, many of the salvaged steel members and pipes will be visible to visitors, establishing clear design connections between the two structures and telling a larger sustainability story.
Learn more about this project in the May/June digital edition of School Construction News, coming soon.